Patented. © All rights reserved. Coverfeed® is a registred and proprietary trademark of Siriuz. Denmark
The keder end is the weakest part
Keders fed into grooves, will eventually experience an unavoidable chafe and tear, ultimately resulting in breakdowns, causing usage delays, frustrations and money. The Coverfeed® models offer:
• Complete protection, eliminating future keder repairs
• No Chemicals or glue/ adhesives needed
• Retrofit and repair on the spot in 2 minutes
• Very durable, hence reliable
• Easy and smooth handling
• Build-in hole for fixtures. No extra webbing and hinges needed
The KCF series - The compact model
This is a compact version of the CF series measuring H: 85 mm, W: 80 mm and D: 10 mm. It is typically installed on roofing surfaces where it has to interact on small areas with other features such as Velcro attachments for side covers, welds etc.
Cutout height: 50 mm
Order Sample here >
The CF series - Multipurpose model
The CF series - measuring H: 145 mm, W: 80 mm and D: 10 mm - is a generic model fitting any plain surfaces. It is typically installed on side surfaces of tents but can also fit roofing areas, if not in dimensional conflict with any fittings, functionality or dimensions. The CF model distributes loads on a wider area than the KCF-series, making it a more generic all-purpose product.
Cutout height: 70 mm
Order Sample here >
The two series in general
Basically, both series do the same: Protect keders and and fixture holes without the need of stitching and webbing. They differ in their geometrical dimensions, due to the fact that various manufacturers have different dimensional standards on different parts of the tents. Fixing the Coverfeed® models are done with the same 10 mm countersunk chipboard screws whatever model desired.
CCF110 and CCF130 in prototype phase
Since we introduced the CF and KCF series - 7,5 mm and 8,5 mm keder diameters - we have continously explore the market needs for new models.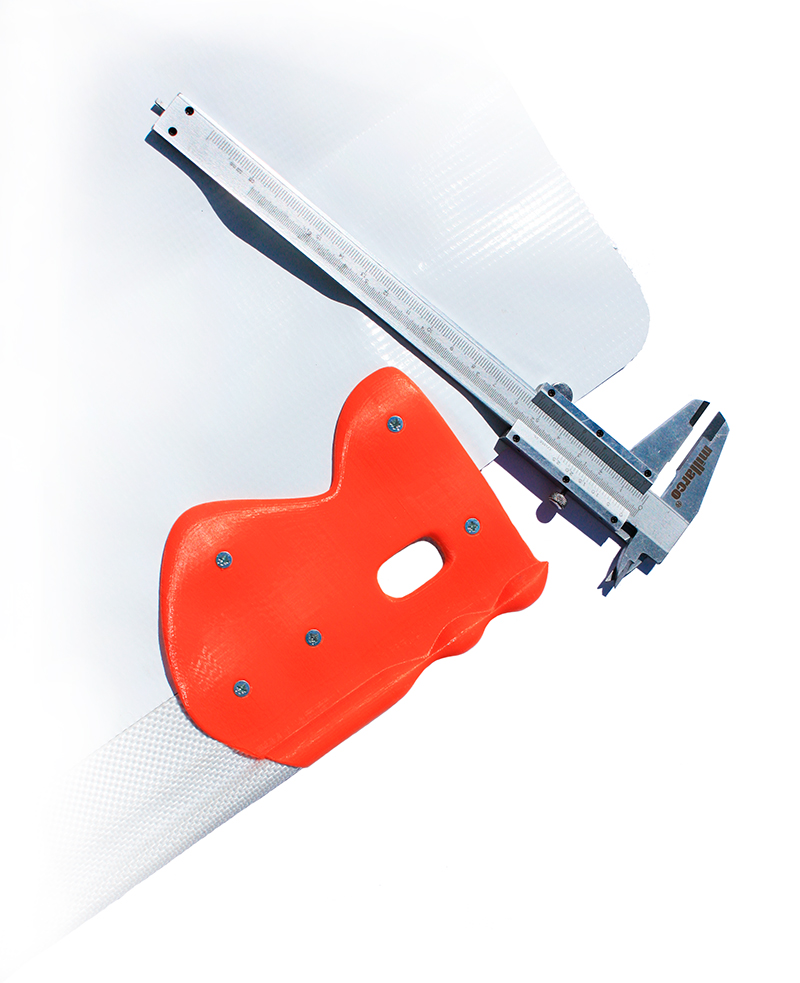
1. Protective edge
The coverfeed® models protects the edge of the textile leading up to the fitting by being covered inside the slit, so battering during installment is kept at a minimum and endurance at max.
2. The Ripple-slug©
The slug going inside the groove is rippled in diameter in order to flex properly, when turning corners in a tent frame’s knee.
3. Fixture by screws
The coverfeed® models are fixed by 5 chipboard screws, piercing through the textile, though not cutting the reinforcing threads inside the textile and compromising strength, making the fixture completely stable. The sockets are countersunk on the screw head side of the Coverfeed® to avoid uneven shapes. See the measurement tables for details and specifications.
4. Reinforced hole for fastening
The hole is designed to accomodate the stresses from pulling the tent with rope from one side of the frame to the other. The edge of the hole is bulging in surface, adding material, distributing the loads evenly over the surfaces.
5. The Spike
The pointy spike allows the keder, when inserted, to be kept in precise aligment to the whole fixture and at the same time solidifying the fixture even more.
6. Keder collar
The keder is protected by a thin collar and fixed by the spike, avoiding exposure of the keder end and fragile leading edge of the textile.
Download
info here >
Made of a versatile Nylon compound
The Coverfeed® models are manufactured by a compound based on a Nylon called Akulon®. The Akulon® polyamides represent the most versatile, well-rounded property profiles of any engineering plastics. It is the ideal material for high performance applications. Robustness, stiffness and high temperature capability make it highly suitable for automotive, electrical and demanding mechanical engineering applications.
Need custom made Coverfeed®?
There are many standards out there and we completely recognize that. The models we market are somewhat generic in dimensions and apply most solutions in the market.
Still, we offer special models for your particular need and dimensions depending on the volume of orders you will invest. Even custom colors can be offered.
Contact
Mikkel Hartvig Andersen > for more information.
Made of a versatile Nylon compound
The Coverfeed® models are manufactured by a compound based on a Nylon called Akulon®. The Akulon® polyamides represent the most versatile, well-rounded property profiles of any engineering plastics. It is the ideal material for high performance applications. Robustness, stiffness and high temperature capability make it highly suitable for automotive, electrical and demanding mechanical engineering applications.
See Akulon®
datasheet here >
High stiffness and strength
At elevated temperatures above 100°C Akulon® maintains good stiffness and strength. Although stiffness of Akulon® decreases sharply around the glass transition temperature (Tg), excellent levels of stiffness are still maintained to just below the melting point of the polymer, facilitating design of critical parts.
Toughness
Akulon® offers outstanding resistance, even in dry as molded conditions, to impacts and shock, down to temperatures of -20°C (-4°F). This is why polyamides are preferred above other engineering plastics. At very low temperatures (-40°C or -40°F), fracture modes become brittle and parts can splinter under impact. For critical safety applications therefore impact modified grades are available in the Akulon® product family offering ductile and hence splinter free impact resistance down to extreme low temperatures.
High elongation at break
Akulon® can be designed with living hinges and snap fits and can accommodate inserts after molding with greatly reduced risk of cracking.
Proven for demanding applications
The combination of mechanical and thermal properties has enabled Akulon® to be used in replacing metals in many applications where durability, safety and part integrity can all be extremely important. Power tool housings, automotive engine intake manifolds, railroad ties, sports equipment bindings, are typical examples where performance, safety, and durability come together and where Akulon® provides the answer through superior and proven performance.
Geometry and design
The Coverfeed® models are designed to meet the geometrical requirements of all major suppliers of extrusions and grooves. The 'Ripple Slug©' (item advanced into groove) is designed to be inserted both forth and back and bend around corners of frames.
The spike (pin lowered into the core keder) cannot break by either stepping on or by normal handling. It will only bend sideways and works to align and solidify the fixture of the Coverfeed® and the keder.
Attaching Coverfeed® to the tent or awning is done by fixing 5 screws in the length of 10 mm (recommended; I.e. Bossard, BN 1426).
Download installation
info here >
Color and UV-resistance
The Coverfeed® is made of white Akulon® Nylon. There are two main reasons for that:
1. Aethstaetics: Since most tents are white, the Coverfeed® will 'fit in' with the general looks and design from all major tent and marquee manufacturers worldwide.
2. UV-resistance: The standard color white is best to reflect the UV from the sun and furthermore, the Akulon® has been mixed with UV-block in the moulding process making it more resistant to UV-radiation, hence less degradable than most plastic products over time. Ordering more than 10.000 units per order, though, give the option to choose freely between any desired colour defined by RAL or Pantone® Color systems, accepting a slightly prolonged delivery time.